Isostatic Presses
Our Contributions
Products We Serve!
Temperature: Room temperature (20–50°C).
Pressure Medium: Water, oil, or elastomeric molds.
Pressure Range: 100–600 MPa.
Key Uses:
Compacting powders (metals, ceramics) into near-net shapes.
Reducing porosity in green bodies before sintering.
Materials: Ceramics, metal powders, polymers, biomaterials.
Advantages:
No thermal stress; ideal for heat-sensitive materials.
Uniform density distribution.
Low energy consumption.
Limitations:
Requires secondary sintering for final densification.
Limited to simple geometries.
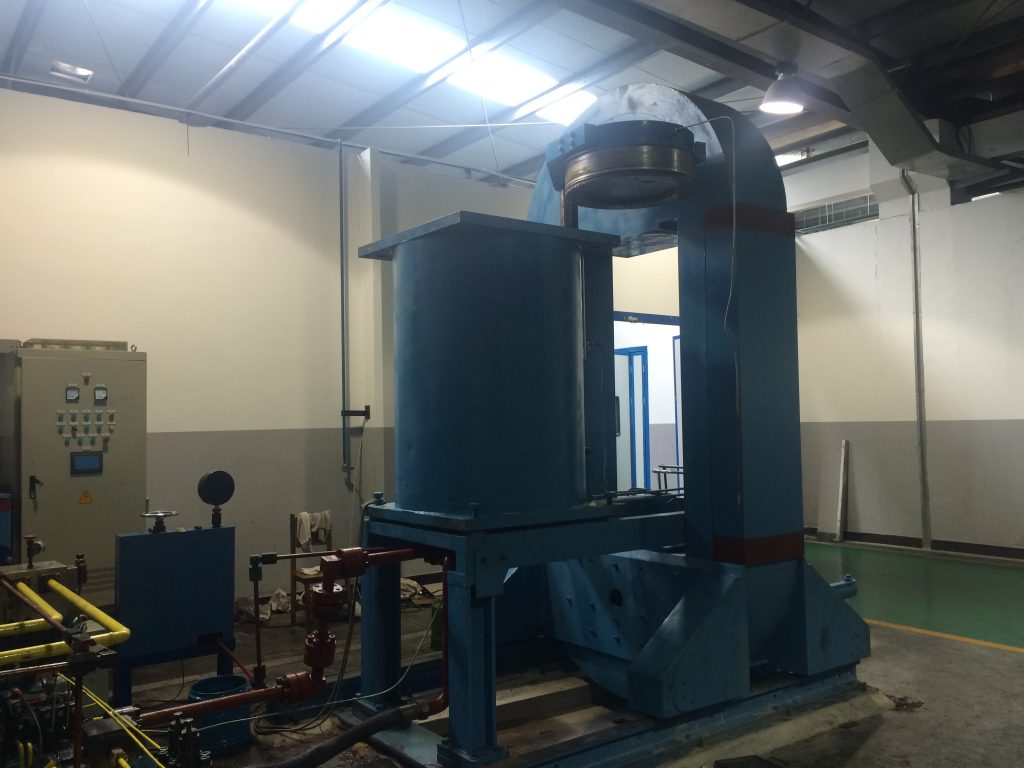
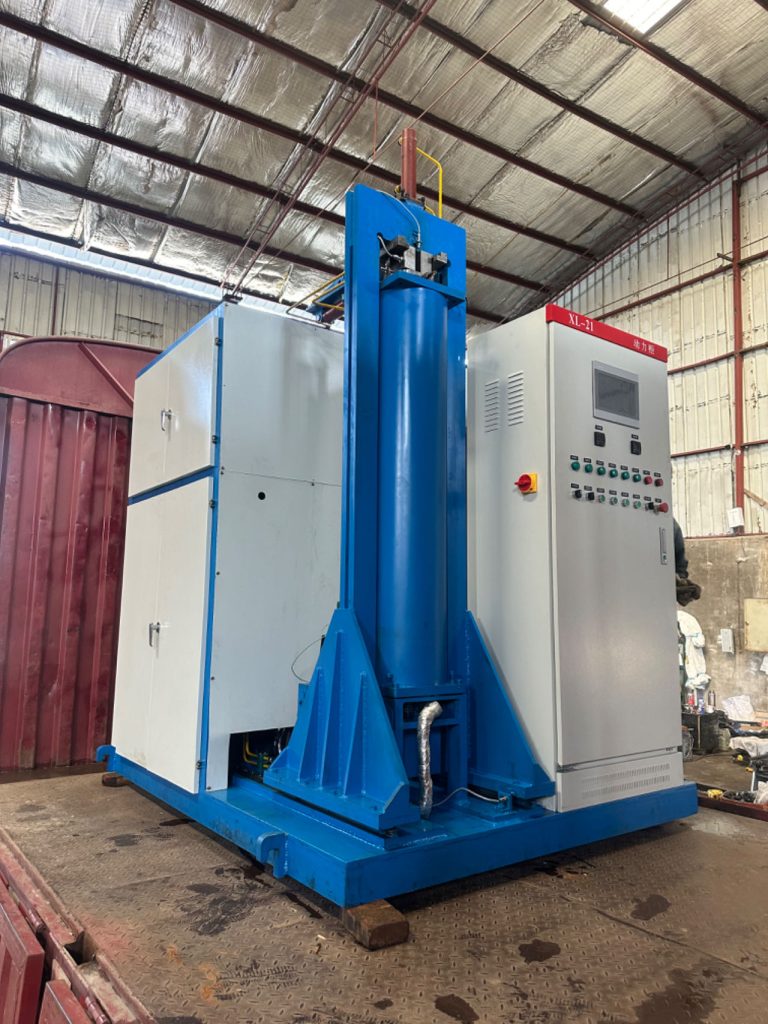
Temperature: Moderate heat (50–300°C).
Pressure Medium: Water (up to 90°C) or oil (higher temps).
Pressure Range: 200–6,000 bar (depending on model).
Key Uses:
Densifying pre-sintered ceramics or composites.
Healing defects in additive-manufactured parts.
Laminating temperature-sensitive electronics.
Materials: Polymers, green ceramics, hybrid composites.
Advantages:
Balances thermal and mechanical effects.
Less distortion than HIP.
Energy-efficient compared to HIP.
Limitations:
Limited to intermediate temperatures.
Not suitable for high-temperature phase changes.
Temperature: Extreme heat (900–2000°C).
Pressure Medium: Inert gas (argon, nitrogen).
Pressure Range: 100–200 MPa.
Key Uses:
Full densification of metals/ceramics.
Eliminating porosity in castings or AM parts.
Homogenizing microstructures (e.g., aerospace alloys).
Materials: Titanium alloys (e.g., TC4),
nickel superalloys (e.g., K403), advanced ceramics.
Advantages:
Achieves near-theoretical density.
Enhances mechanical properties
(creep resistance, fatigue strength).
Limitations:
High energy and operational costs.
Complex equipment and safety requirements.
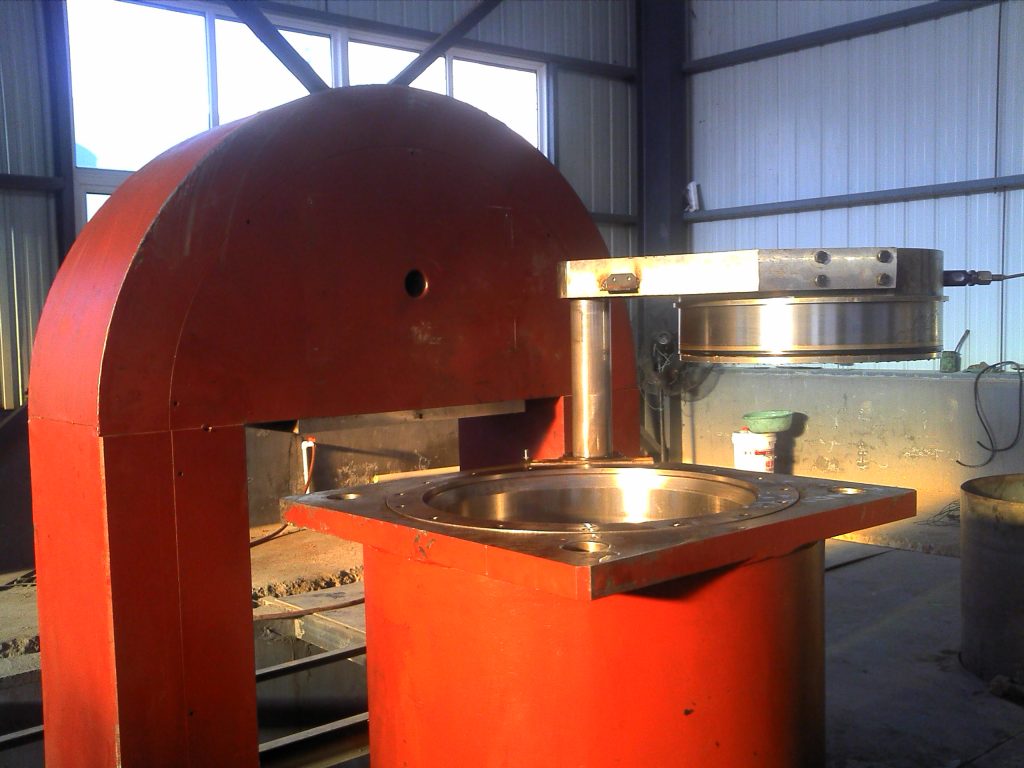
Comparison Table
Feature | CIP | WIP | HIP |
---|---|---|---|
Temperature | 20–50°C | 50–300°C | 900–2000°C |
Pressure Medium | Water/oil | Water/oil | Inert gas (Ar, N₂) |
Primary Goal | Shape forming, green-body compaction | Defect healing, moderate densification | Full densification, phase transformation |
Energy Use | Low | Moderate | Very high |
Typical Materials | Ceramics, metal powders | Pre-sintered ceramics, composites | High-performance alloys, ceramics |
Post-Processing | Requires sintering | May require sintering | Often final product |
As leaders in high-pressure technology, we specialize in the design and manufacturing of advanced Isostatic Presses. Our systems—both Hot Isostatic Presses (HIP) and Cold Isostatic Presses (CIP)—are engineered to achieve full densification of powdered metals, ceramics, and composites, or to eliminate internal porosity in castings and 3D-printed metal parts. The result is components with superior material integrity, enhanced mechanical properties, and unparalleled reliability.
Custom-Engineered HIP and CIP Systems
We recognize that no single solution fits every application. That is why we are dedicated to providing fully customized Isostatic Presses tailored to your specific process requirements. Our engineering team works closely with you to define critical parameters, including:
Vessel Size: From compact laboratory presses for research and development to massive production systems with working zones several meters in diameter.
Pressure & Temperature: We design systems to achieve a wide range of pressures (up to 30,000 PSI / 200 MPa or higher) and, for HIP systems, temperatures exceeding 2,000°C.
Control Systems: We offer advanced, intuitive PLC-based control systems for precise cycle management, data logging, and operational safety.
Over 30 Years of Proven Manufacturing Expertise
The foundation of our company is our people. Our core technical and manufacturing team possesses over 30 years of hands-on experience exclusively in the isostatic pressing industry. This deep institutional knowledge translates directly into robust, safe, and efficient machine design. We have a profound understanding of the critical nuances of high-pressure vessel engineering, adherence to international safety codes (like ASME), and the complex interplay between materials, pressure, and temperature. This expertise ensures that every press we build is not only powerful and precise but also built to last.
By combining our deep-rooted experience with a commitment to custom engineering, we deliver Isostatic Presses that are complete, reliable solutions for today’s most demanding manufacturing challenges.
Our technical team has successfully developed and implemented numerous technological enhancements for isostatic presses. These innovations have been officially recognized and granted the following Chinese utility model patents:
Searchable on both the European Patent Office (EPO) and the China National Intellectual Property Administration (CNIPA) websites:
Publication No.: CN210308318U (Application No.: 201920430348.2)
Publication No.: CN210308319U (Application No.: 201920908293.1)
Publication No.: CN210308454U (Application No.: 201920907463.4)